Machines are subject to wear due to friction between moving parts. The expensive heavy equipment, such as wind turbines and aircraft propellers, are expensive to shut down or repair. Researchers at the George Washington University have developed a real-time sensor and nanotechnology-based system that detects the component surface damage in moving parts, such as gears, and repairs and sustains the moving parts of the machines automatically.
The self-repairing system enables the machines that are long-lasting and self-sustaining. The invention deploys a monitoring system of thin film automatic sensors to monitor physical metallurgical conditions of machine’s moving parts on their surfaces. The sensors transmit monitoring data using radio signals to a control site. The system also comprises a mathematical model that identifies damage through anomaly pattern recognitions and generates distress signals that trigger repairing process. Ultimate aim of the system is to reduce premature failures of machines such as expensive wind turbines and aircraft propellers, labor cost and maintenance downtime significantly. This invention may have a profound effect on how machines are designed, built and maintained.
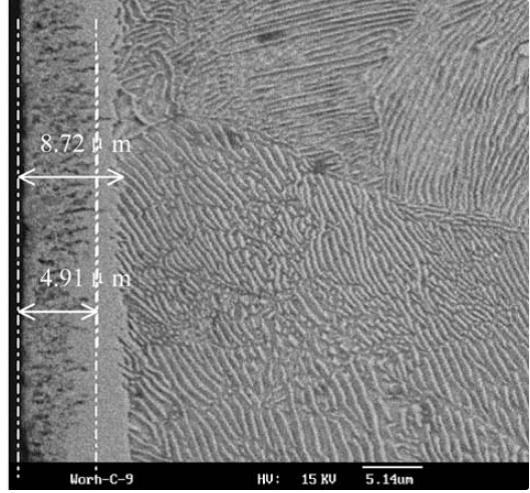
Figure: The repaired surfaces in a diesel engine cylinder by optical and SEM micrographs.
Applications:
- Self or autonomous repair and maintenance of heavy machines, such as windmills and aircraft engines.
- Autonomous repair module can be built into heavy machines or installed into existing machines such as windmills and jet engines.
Advantages:
- Minimizes downtime of expensive machines that are very expensive to repair
- Autonomous repair module envisioned in this invention will reduce the downtime and maintenance costs of heavy machines.