Precision timing control of thruster operation of a spacecraft employing electric propulsion methods (e.g., pulsed electromagnetic plasma thrusters) is vital for space missions, and also difficult to achieve. When a thruster fires longer (or more powerfully), or shorter (or less powerfully), than required, or is fired in imprecise synchronization with other thrusters, an error can be calculated and the next cycle of thruster operation has to be adjusted to minimize the cumulative error to acceptable limits. In an Electronic Propulsion (EP) system, specifically vacuum arc thrusters utilizing a pulsed mode of operation, plasma pulses are expected to be regular in nature, yet this is often not the case. Minute variations in the electrical, thermal, and/or, mechanical behavior of the thruster head after repeated operation over the lifetime of the component are not given adequate consideration in commercially available control systems and shorten the lifespan of EP spacecraft.
Researchers at The George Washington University have developed a control system to achieve precision control of various electronic propulsion subsystems. Features of the available control system (currently at NASA Technological Readiness Level 7 and manifested for on-orbit demonstration in 2015) include:
- a programmable control system based upon embedded computers; a fast algorithm to define and manipulate timing marks of high-frequency low-level logic/analog events;
- a method to generate, adjust and synchronize pulse-width-modulation capable event triggers over diverse control channels, without a need for direct feed-back control loop,
- interfaces for synthesizing the low-level timing elements of all such actions in relation to a very accurate timing relationship with external events expected to be ongoing in a spacecraft mission.
By adopting a programmable, embedded, systems approach, sub-nano second accuracy of the impulse-bits can be achieved, with the capability to change the operating modes/parameters within the span of a fraction of a single impulse-bit cycle, on either a pulse-by-pulse, or event-driven basis. The overall system architecture assumes, and is designed for, the constant recalculation of required low level tasks for generating impulse bits (responsible for causing minute changes of momentum) during each cycle. Programming features allows the modification of the entire system behavior, including modifying the software protocol, to compensate for any physical changes to the system over time as may be required for a deep space, long duration mission. In this manner, GW researchers have extended the accuracy of control methods and the mission longevity of EP powered spacecraft.
The hardware elements of the core system can also be simultaneously applied to high frequency, agile control systems, for complex non-propulsion avionics, ADCS, GN&C, EPS, Communications and industrial/robotic/automation applications.
Additional Fields:
- Automotive Industry: Engine control systems
- Avionics, Industrial Automation, Scientific industries, Control Systems
- Semiconductor Industry: ASIC, FPGA, Embedded Computing elements
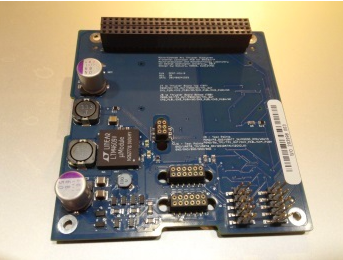

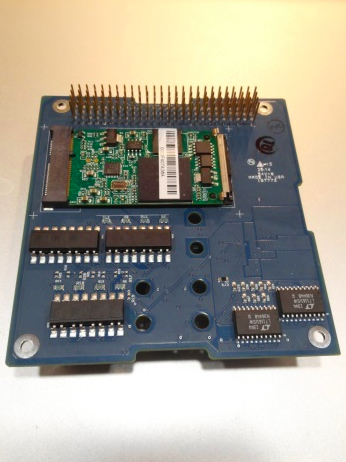
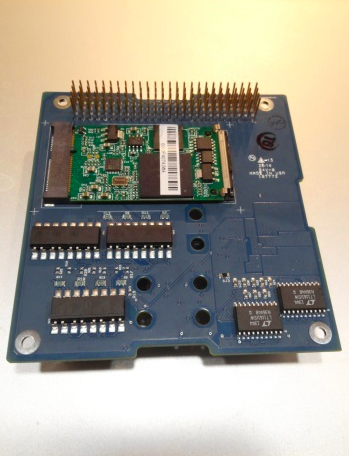
Applications:
Advantages:
- Provides fine control over electronic propulsion systems
- Improved efficiency with improved control extends thruster life
- Highly efficient software saves power for thrusters