There is a need for a new process for encapsulating complex chemical additives, where microcapsules can give strong performance under hostile chemical and mechanical conditions. While microencapsulation technique is a mature technology, microcapsule products made by traditional techniques may work well only in relatively simple, passive and non-hostile conditions. On the other hand, in engine lubrication applications, both additives to be encapsulated and the surrounding solution may exhibit complex chemistry. Furthermore, lubrication often operates at high temperature, high pressure, and high shearing environments where microcapsules made by traditional techniques simply do not work well.
GW researchers have developed a novel process for microencapsulating complex chemical additives suitable for operating at high temperature, high pressure, and high shearing lubrication environment. To prepare such microcapsules, GW researchers carefully controlled parameters such as pH, temperature, reaction sequences, cooling, and polymer chemistry during the microencapsulation process. GW researcher discovered that microcapsules made by the new process are surprisingly tough and chemically resistant than previously known microcapsules. As a result, such microcapsules can withstand lubrication environments well and can provide a more timed and controlled release of additives than traditional microcapsules.
In addition to lubrication, this novel microencapsulation process can be used as process fluids and coolants that require optimal performance at similarly hostile chemical and mechanical environments.
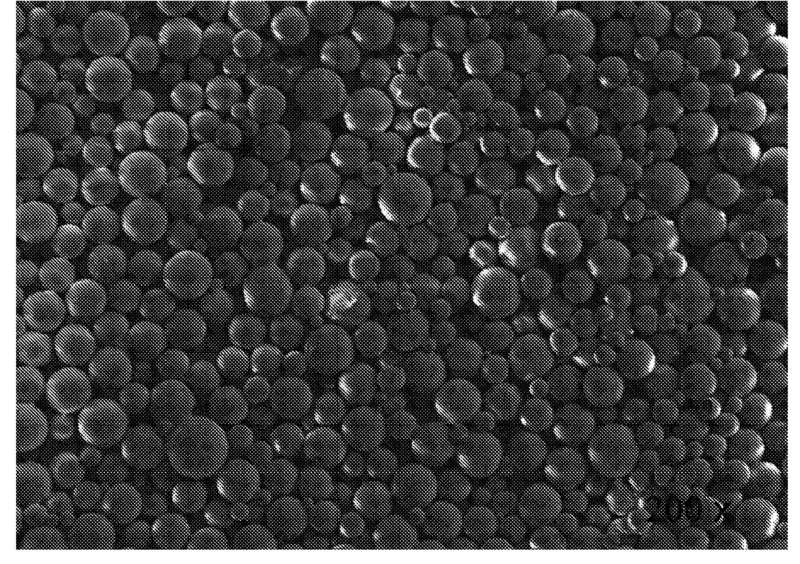
Application:
A novel microencapsulation process where microcapsules exhibit high performance under harsh chemical and mechanical operating environments and thus suitable for lubrication.
Advantages:
Microcapsules made by the novel process can:
1. Encapsulate multiple complex chemical additives
2. Avoid deleterious chemical interactions during use
3. Deliver the desired chemistry at the right time and the right place
4. Achieves optimal lubrication performance